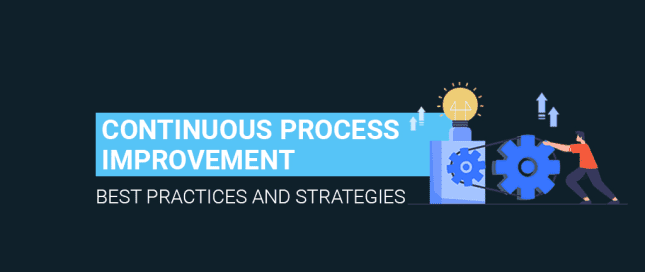
TABLE OF CONTENTS
- 1. Overview of Continuous Improvement
- 2. What is the Goal of Continuous Improvement?
- 3. When Should You Optimise Your Processes?
- 4. Business Gains of Implementing Proven Process Improvement Strategies
- 5. Top Continuous Improvement Methodologies
- 6. Key Aspects of Continuous Improvement
- 7. Checklist to Help You Implement a Continuous Improvement Culture
- 8. 6 Strategies for Leaders to Create a Culture of Continuous Improvement
- 9. 4 Powerful Techniques to Drive Continuous Process Improvement
- 10. How BPM Software Helps Establish a Continuous Improvement Culture
- 11. Continuous Improvement: Real-World Benefits
- 12. Start Your Continuous Improvement Journey
- 13. FAQs
What’s stopping your business from performing at its absolute best? Is it slow approvals, manual workarounds, duplicated tasks, or outdated processes no one questions anymore? Most businesses lose significant time, money, and value simply because they don’t embed continuous improvement into their operations.
Research by McKinsey shows that organisations applying rapid experimentation and continuous improvement best practices can boost productivity by 25% or more. That’s not just tweaking workflows—it’s a complete mindset shift with real impact.
If you’re nodding along, it’s time to treat improvement not as a one‑off project but as an ongoing strategic priority. Continuous improvement is about systematically fine‑tuning processes to stay competitive, agile, and aligned with your evolving goals.
This blog will take you on a deep dive into proven best practices and smart strategies: from detecting inefficiencies early, to fostering cross‑functional collaboration, to harnessing data for faster, smarter decisions.
Overview of Continuous Improvement
Continuous Improvement is a philosophy and practice aimed at constantly enhancing processes, products, or services within an organisation. It emphasises the incremental refinement of systems and procedures to achieve greater efficiency, effectiveness, and quality. At its core, Continuous Improvement fosters a culture of innovation, collaboration, and adaptability, enabling businesses to thrive in dynamic environments.
One of its key principles is pursuing perfection through small, iterative changes. Rather than waiting for major overhauls, organisations focus on identifying areas for improvement and implementing incremental adjustments. The approach of going from small-level improvements to large ones allows organisations to progress without disrupting operations or causing excessive costs.
To take full advantage of continuous improvement, you need commitment from all levels of an organisation, from leadership to frontline employees, while implementing continuous improvement. It involves fostering a culture of open communication, where feedback is encouraged, and ideas for improvement are heard and discussed. By empowering employees to contribute to the improvement process, organisations harness the collective intelligence and creativity of their workforce.
Furthermore, improving your business processes continuously can give your organisation a competitive advantage, which is necessary to ensure long-term success. It refines how your business process functions and delivers your customers great value, which eventually helps you to stay ahead of the curve and adapt to ever-changing market demands.
To facilitate the continuous improvement journey, many forward-thinking organisations leverage BPM tools such as PRIME BPM. These software solutions are pivotal in tracking performance metrics and pinpointing areas ripe for improvement. Integrating such tools not only simplifies the monitoring process but also provides actionable insights that empower decision-makers to make informed adjustments.
What is the Goal of Continuous Improvement?
In any organisation, the goal of continuous improvement is to create a culture where enhancement is always on the agenda. You might have spent a lot of time crafting process maps to optimise your operations. However, it’s common to forget about them once they’re in place. Focus on continuous improvement can change that. It helps keep your processes under constant review, making sure they’re always evolving to meet your needs.
By embracing the best practices, you and your team can actively engage with your process maps. This means spotting inefficiencies, identifying bottlenecks, and finding areas that need improvement. With this approach, you can make small changes, test them out, and adjust as necessary.
What’s more, continuous improvement encourages you to take a proactive approach to innovation and adaptation. This means you’re always ready to respond to changes in the market and the needs of your customers. The goal isn’t just to create static process maps; it’s to use them as dynamic tools to drive excellence and ensure long-term success for your organisation.
Take a look at this quick video by a BPM industry expert to know how mapping and forgetting can become a roadblock to your continuous improvement journey.
Take a look at this quick video by a BPM industry expert to know how mapping and forgetting can
become a roadblock to your continuous improvement journey.
When Should You Optimise Your Processes?
Here are some key signs you can’t afford to ignore:
High Error Rates
When error rates start to increase, it’s a clear sign that existing processes may be flawed or inefficient. Addressing these issues promptly can prevent further errors and improve overall performance.
Decreased Productivity
A noticeable decline in productivity among employees indicates that current processes may be hindering rather than enhancing workflow. Streamlining processes can help boost productivity and output.
Rising Costs
If operational costs are on the rise without a corresponding increase in revenue, it’s time to reevaluate and optimise business processes to eliminate waste and improve cost-effectiveness.
Customer Complaints
An increase in customer complaints often points to inefficiencies or shortcomings in business processes. Addressing these issues can enhance customer satisfaction and loyalty.
Long Lead Times
Lengthy lead times from order placement to delivery can indicate inefficiencies in production or service delivery processes. Optimising these processes can reduce lead times and improve customer satisfaction.
Regulatory Changes
Changes in regulations or compliance requirements may necessitate updates to existing processes to ensure adherence and avoid penalties or legal issues.
Growth or Expansion
Business growth or expansion often requires scaling existing processes to accommodate increased demand. Reviewing and optimising processes can support sustainable growth and scalability.
Competitive Pressures
Increased competition may necessitate process improvements to stay ahead in the market. Businesses should continuously evaluate and enhance processes to maintain a competitive edge.
Recognising the Need for Standardisation
Inconsistent procedures across departments or locations can lead to confusion and inefficiencies. Recognising the need for standardisation ensures consistency and improves overall process effectiveness and efficiency.
Technology Advancements
Advancements in technology, like implementing BPM software, offer opportunities to ease the method of performing tasks and improve efficiency. Businesses should regularly assess their processes to leverage new technologies effectively.
Business Gains of Implementing Proven Process Improvement Strategies
Continuous process improvement is a strategic journey that offers numerous benefits for your organisation. It involves identifying and eliminating inefficiencies and bottlenecks within your business processes to create streamlined workflows. Here’s how it can benefit you:
Reduced Costs
By systematically addressing inefficiencies, you can cut operational costs, optimise resource utilisation, and achieve significant savings across your operations.
Faster Processing
Streamlining workflows leads to faster processing times, reducing delays and improving overall efficiency in delivering products or services to your customers.
Fewer Errors
Continuous refinement reduces the likelihood of errors, enhancing the quality and accuracy of your outputs, which increases customer satisfaction and trust.
Better Quality End Products
As you fine-tune processes, you enhance the consistency and precision of your outputs, positioning your organisation favourably in the market.
More Productive Employees
Empowering employees to participate in improvement boosts morale and productivity, as they see their input leading to positive changes.
Happier Customers
Improving efficiency, reducing errors, and delivering higher-quality products or services creates a positive customer experience, leading to increased satisfaction and loyalty.
The specific benefits that your organisation can reap from continuous improvement depend on its focus areas within the improvement initiative. Currently, 70% of firms concentrate on boosting productivity and lowering costs, while 38% aim to increase customer satisfaction and 35% focus on product improvement, reflecting a holistic approach to enhancing overall operations.
Top Continuous Improvement Methodologies
Continuous Process Improvement encompasses a variety of methods and approaches designed to systematically enhance organisational processes. Some of the prominent methods include:
Business Process Management
BPM is a methodology of comprehensively documenting, analysing, optimising and monitoring workflows. All these are the essential components to create a culture of continuous improvement in an organisation. Managing business processes efficiently boosts productivity, cuts expenses, and upholds quality standards. It fosters agility and innovation, empowering organisations to adapt swiftly to market changes and customer demands for sustained success.
Six Sigma
Six Sigma is a data-driven methodology that focuses on minimising defects and process variations. It involves defining, measuring, analysing, improving, and controlling processes (DMAIC). By using statistical BPM tools and techniques, organisations can identify and eliminate defects, leading to improved quality and efficiency.
Lean Management
Originating from manufacturing principles, Lean Management aims to eliminate waste and increase efficiency. Key principles include value stream mapping, 5S (Sort, Set in order, Shine, Standardise, Sustain), and Kanban. Lean encourages a culture of continuous improvement by empowering employees to identify and eliminate non-value-added activities.
Total Quality Management (TQM)
TQM is a holistic approach that involves the entire organisation in the pursuit of quality and customer satisfaction. It emphasises customer focus, continuous improvement, and employee involvement. TQM principles include process mapping, benchmarking, and the Plan-Do-Check-Act (PDCA) cycle.
Kaizen
Kaizen is a philosophy, originating in Japan, that emphasises continuous, incremental improvement. It encourages small, manageable changes made by employees at all levels. Kaizen events or workshops bring cross-functional teams together to analyse and improve specific processes.
Key Aspects of Continuous Improvement
Continuous Improvement embodies three essential elements, all pivotal for your organisation’s growth and excellence.
1. Process Improvement | Refine and optimise operational processes by identifying inefficiencies, streamlining workflows, and eliminating bottlenecks. Utilise methodologies like Lean and Six Sigma for systematic analysis and improvement. |
---|---|
2. Product Improvement | Evolve products or services through iterative development, incorporating feedback, and fostering innovation to meet changing customer needs and market demands. Enhance product quality, functionality, and value proposition. |
3. People Improvement | Develop and empower individuals within the organisation through employee training, skill development, and nurturing a culture of collaboration and innovation. Engaged employees are the driving force behind organisational excellence. |
While these aspects operate in distinct ways, their singular objective remains steadfast: to monitor current operations and strategise improvements aimed at delivering the utmost value to customers.
Checklist to Help You Implement a Continuous Improvement Culture
Here’s how you and your organisation can approach continuous improvement, broken down into four stages—Plan, Do, Check, Act:
1. Plan |
|
---|---|
2. Do |
|
3. Check |
|
4. Act |
|
Watch this expert interview for real-time actionable insights on Establishing a Culture of Continuous Improvement.
4 Powerful Techniques to Drive Continuous Process Improvement
Continuous Process Improvement is a fundamental aspect of enhancing organisational efficiency and effectiveness. Let’s delve into 4 practical techniques to drive Continuous Process Improvement in an organisation:
Process Mapping
Process mapping involves creating a visual representation of a workflow, providing a clear and comprehensive view of each step in a process. By systematically outlining processes, organisations can identify inefficiencies, redundancies, and areas for improvement. Process mapping fosters collaboration among teams, aligns stakeholders, and serves as a foundation for continuous improvement.
This quick video will help you learn how to gather process information to ensure accurate process mapping.
Root Cause Analysis
Delving beyond surface-level issues, root cause analysis allows organisations to pinpoint the fundamental reasons for challenges. Addressing these root causes ensures long-term solutions, preventing recurrent issues and promoting sustained improvement. To identify the root cause of a problem, ask these five questions:
- What happened?
- When did it happen?
- Who was involved?
- What were they doing?
- What were the circumstances?
By answering these questions, the team can uncover the primary causes of bottlenecks and inefficiencies. This deep dive into the root causes provided valuable insights necessary for crafting targeted improvement strategies.
Waste Reduction
Waste reduction involves eliminating unnecessary steps, resources, or activities that do not add value to the end product or service. This is an effective continuous improvement technique as it involves optimal resource utilisation, cost savings, and a more agile response to evolving business needs.
Value-Added Analysis
Value-added analysis involves assessing each step in a process to determine its contribution to the final product or service and identifying areas that add value to either the customer or business. Value-added analysis helps in continuous process improvement as it helps eliminate or reduce non-value-adding activities. This approach guides decision-making, encourages innovation, and ensures that resource efforts contribute directly to organisational objectives and customer satisfaction.
Watch this quick video to learn how to undertake value-added analysis.
6 Strategies for Leaders to Create a Culture of Continuous Improvement
Creating a culture of continuous improvement within your organisation is crucial for staying ahead in today’s competitive landscape. Here are some practical tips to cultivate this culture effectively:
1. Be the Part of Improvement Journey
Your team doesn’t just take cues from what you say; they’re inspired by what you do. As the leader of your organisation, it’s crucial to set the right example. Instead of simply issuing directives, get involved with your team in the process of improvement. Even, when assembling a team to drive continual enhancement, select individuals who share the same ethos. By demonstrating that improvement is a priority for the leadership, you signal its importance to everyone else, motivating them to invest their own time and effort.
2. Involve your Team and Take Suggestions
Have you wondered why some startups just become large companies in just a few years? The secret sauce behind their growth is they follow the right path to implement the ideas that their employees give – even the bad ones. They recognise that even seemingly flawed suggestions can lead to genuine opportunities by steering employees toward better solutions. To foster a culture of ongoing refinement, establish a policy of swift response to all suggestions. Either green-light the proposed idea for implementation or guide your employees in refining it further to address the underlying problem.
3. Schedule Time to Communicate Ideas
Too often, leaders solicit ideas from their team members but fail to allocate time for meaningful discussion. You need to understand that continuous improvement should be part of daily activities and as a leader, it’s your job to empower your employees to make daily continuous improvement a part of their work every day. This means you need to get in touch with them regularly to listen to their thoughts and help them secure the time and resources they need to do so. By fostering an environment where idea sharing and implementation are prioritised, you empower your team to drive countless improvements every day.
4. Consider All Types of Improvements
While it’s tempting to focus solely on addressing issues that directly impact the bottom line, don’t overlook the value of small-scale improvements. For example: enhancements in efficiency or employee engagement may seem minor, but they can have a significant cumulative effect over time. Starting with these smaller, quick-win improvements demonstrates your commitment to progress and also boosts morale among your team. Witnessing tangible results from their efforts motivates employees to tackle larger challenges with increased enthusiasm and dedication.
5. Invest in Tools and Training
Investing in the right tools facilitates broader participation, accelerates the pace of change, engages leadership, and breaks down organisational silos. However, investing in tools alone isn’t sufficient; you must also provide comprehensive training to your team to ensure they can effectively leverage the benefits of these tools. Empowering your employees with the necessary skills and resources sets the stage for sustained growth and innovation within your organisation.
6. Keep Monitoring the Performance and Reward Small Wins
Team members feel motivated, and inspired to continuously strive for excellence, when they are appreciated for their efforts. Appreciation doesn’t have to be reserved for significant achievements alone. Recognising even small efforts and incremental improvements sends a powerful message that every contribution matters and is valued. So, remember to express your gratitude and admiration for the efforts of your team members regularly.
How BPM Software Helps Establish a Continuous Improvement Culture
By streamlining processes and pinpointing bottlenecks, Business Process Management software plays a crucial role in cultivating a culture of ongoing refinement. Here’s how BPM software facilitates Continuous Improvement:
Process Optimisation
BPM software excels in minimising manual tasks and enhancing process efficiency. By optimising workflows using analytic tools, you can eliminate bottlenecks, reduce processing times, and improve overall operational speed and accuracy. It can boost productivity and lay a strong foundation for continuous improvement efforts.
Data-Driven Decision Making
For effective continuous improvement, timely and accurate data is essential. BPM software facilitates data collection, analysis, and reporting features which can help you get valuable insights into your processes. With real-time data, you can easily identify areas for improvement, track performance metrics, and make informed decisions to drive continuous enhancements.
Identifying Inefficiencies in Current Processes
BPM software allows you to visualise end-to-end processes through intuitive mapping and modelling features. It helps you identify inefficiencies, redundancies, and bottlenecks in your current processes. By analysing these visual representations, you can pinpoint areas for improvement and strategically plan enhancements as part of your improvement initiative.
Collaboration and Communication
Effective communication and collaboration are vital for successful ongoing enhancement projects. BPM software offers a centralised platform for collaboration, enabling teams to work seamlessly on process improvements. By fostering transparent communication and collaboration, BPM software ensures that all stakeholders are aligned and engaged to achieve the goal of your improvement project.
Monitoring and Performance Measurement
Continuous Improvement requires ongoing monitoring and performance measurement. The software provides robust monitoring tools that track key performance indicators (KPIs) and offer real-time analytics. These tools allow you to assess the impact of implemented changes, identify areas needing further improvement, and measure the success of your continuous improvement initiatives over time.
Flexibility for Process Changes
Continuous improvement involves adapting to changing business environments and evolving customer needs. BPM software offers the flexibility needed to implement and manage process changes seamlessly. Whether you’re tweaking existing processes or incorporating major process innovations, BPM software ensures that you can quickly and effectively adapt to the evolving demands of the business landscape.
Continuous Improvement: Real-World Benefits
So how does Continuous Improvement deliver in real life? Let’s look at a success story.
A medium-sized regional council in Victoria embarked on a transformative journey towards continuous improvement. With over 300 employees serving 30,000 residents, the council aimed to streamline operations and enhance productivity across various service sectors, including roads, infrastructure, public health, and more.
Challenges initially included operational inconsistencies, lack of clarity on automation needs, hidden operational costs, and procedural ambiguities leading to customer complaints.
Through meticulous process mapping and evaluation, the council identified areas ripe for improvement. Implementation of new work practices and technological interventions resulted in remarkable outcomes. Efficiency gains of 173 hours per year were realised in debt collection, equating to a savings of $7,785. Additionally, the supplier validation process saw a 50% reduction in processing time, contributing to significant time and cost savings. With clearer visibility into operational costs, the council estimated an annual saving of $35,532. Furthermore, efficiency in customer refund processing soared by 90%.
By fostering a culture of continuous improvement, the regional council not only optimised its operations but also enhanced service delivery to the community, laying a strong foundation for future growth and innovation.
Watch this quick video of another case study on how embarking on a continuous improvement journey using BPM software helped the first Filipino life insurance company achieve their business goals.
Start Your Continuous Improvement Journey
Continuous Process Improvement is a dynamic method vital for ensuring optimal performance in organisational processes. It is obvious that avoiding process stagnation and embracing continuous improvement is critical. Organisations can adopt several techniques for improvement, but they should select methods based on how their teams are already operating to promote a continuous improvement culture.
Leveraging the right tools is not just an option; it’s a strategic approach for organisations aspiring to thrive in an ever-evolving business landscape. PRIME BPM software is a robust BPM solution, offering features such as standard process documentation, rapid process mapping, one-click analysis, and collaborative capabilities. The tool empowers businesses to undertake end-to-end improvement journeys seamlessly.
Based on powerful methodologies, such as BPM, Lean, Six Sigma, Value Stream Mapping and more, PRIME BPM has helped hundreds of leading organisations embark on their continuous improvement journeys. Check out some success stories.
To experience the powerful features and functionalities of PRIME BPM, take the first step with a 15-day free trial and unlock the potential for sustained excellence in your operational endeavours.
FAQs
Sustaining Continuous Improvement efforts requires integrating improvement practices into the organisational culture, regularly monitoring progress, fostering a supportive environment for innovation, and continuously learning and adapting to new challenges and opportunities.
Common challenges in implementing Continuous Improvement include resistance to change, lack of leadership support, insufficient resources or expertise, unclear goals or priorities, and difficulty sustaining momentum over time. Addressing these challenges requires a coordinated effort and a willingness to learn and adapt.
Continuous Improvement can benefit various departments within an organisation, including operations, marketing, sales, customer service, human resources, and finance, by improving processes, enhancing productivity, reducing costs, and ultimately delivering better products or services to customers.
Technology plays a crucial role in Continuous Improvement. Advanced BPM tools such as PRIME BPM enable data collection, analysis, and visualisation, facilitating collaboration and communication among team members, and streamlining processes for greater efficiency.
PRIME BPM offers a comprehensive end-to-end platform with built-in methodology to drive continuous improvement, featuring intuitive process mapping, analysis tools, and collaboration capabilities. With its user-friendly interface and robust functionality, PRIME BPM simplifies the implementation process, fosters team engagement, and enables organisations to drive sustainable improvement across their operations effectively.